Samen met mijn zoon Floris ben ik in 2019 begonnen met de bouw de LTM 30 locomotief voor spoor 1 naar het ontwerp van Pim van Schaik. Hoe lang de bouw gaat duren, weet ik nog niet. Maar het is fantastisch te zien hoe Floris enthousiast is.
In juli 2019 hebben we de tekeningen van de locomotief bij modelbouwtekeningen.nl besteld. We zijn nu aan het bouwen. De bedoeling is om Floris zoveel mogelijk te betrekken bij de bouw, maar aan de grote machines vindt ik hem nog een beetje te klein. Uiteindelijk ben ik uiterst voorzichtig met hem.
Over de locomotief
In de periode 1922-1925 bouwde de Hannoverische Machinenfabrik AG (Hanomag) de loc serie 21 – 35 voor de normaalspoor lijnen van de Limburgsche Tramweg-Maatschappij (LTM). De locs deden dienst op de normaalsporige lijnen in Zuid-Limburg: Maastricht-Vaals (Zijlijn naar Wijle) en Roermond-Sittard (Met vier korte zijlijnen). De los 21 en 34 werden voor 1938 reeds afgevoerd, de over gebleven locs werden bij de opheffing van de LTM verkocht, waarbij twaalf locs naar de Maastrichtse Metaalhandel H.E. Dotremont (welke praktische al het materieel van LTM opkocht) en één loc naar de Staatsmijnen (later via Dotremont nog twee).
De 26 werd verkocht aan Klöckner & Co in Duitsland, waar deze tot 1949 heeft dienstgedaan. Na verkoop aan Sachtleben Chemie werd de loc in 1954 weer rijvaardig gemaakt en heeft tot 1972 dienstgedaan. In 1972 werd de loc door de Tramweg-Stichting gekocht en terug naar Nederland gehaald, waarna de loc na een revisie in 1974 als LTM 21 (omdat men in de veronderstelling was dat dit de LTM 21 betrof) bij de Museumstoomtram Hoorn – Medemblik in gebruik werd genomen. Tijdens een restauratie in 2000 werd ontdekt dat het de LTM 26 betrof, waarna de locomotief na de restauratie het correcte nummer terug kreeg. In onderstaande tabel zij de technische gegevens opgenomen van de locomotieven.
Tractievorm | Stoom |
Fabrikant | Hannoverische Machinefabrik AG, Hannover Duitsland |
Type | Stoomtramlocomotief |
Gewicht | 28,5 ton |
Lengte over buffers | 6,73m |
Asindeling | Bh2t |
Maximum snelheid | 60 km/uur |
Tractiedetails | Verhoop stoomverdeling |
Oorspronkelijke | Limburgse Tramweg Maatschappij (LTM) |
Het model
Het model is gebaseerd op de tekeningen van de LTM30 zoals getekend door Pim van Schaik en te verkrijgen via www.modelbouwtekeningen.nl. Het betreft een spoor 1 model, oftewel een spoorbreedte van 45mm.
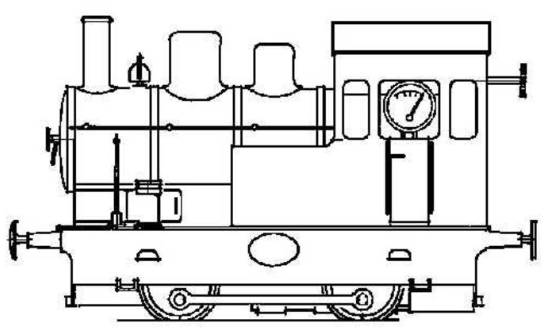
Zelf ben ik de locomotief aan het tekenen in Onshape. Dit om meer een gevoel te krijgen hoe de locomotief te maken en om hier en daar een (kleine) wijziging door te voeren.
De bouw
Ketel
We zijn begonnen met het maken van de ketel. We maken hierbij gebruik van het ontwerp van de tweede versie ketel van Pim van Schaik. Het betreft een ketel met twee waterpijpen en aan de onderzijde stekels waar het vuur tegen aan komt.
De romp is gemaakt van 35mm koperbuis. De buis is afgedraaid zodat de wanddikte gereduceerd is tot circa 1 mm.
Voor het boren van de gaten in de ketelromp heb ik een opstelling gemaakt van hout zodat ik de romp in de juiste positie kon draaien. Floris heeft meegeholpen met het boren. Nadat ik het werkstuk in de juiste positie had gezet, mocht Floris voorzichtig de gaatjes boren.
De frontjes hebben we gemaakt van het koperbuis materiaal. Hiervoor heeft Floris de buis in de lengte open gezaagd. Hebben we samen het koper roodgloeiend gemaakt en heeft Floris het koper platgeslagen. Floris heeft vervolgens de rondjes voor de frontjes uitgezaagd.
Ik heb een mal en contramal gemaakt voor de frontjes. Floris heeft veel geduld gehad om de frontjes te voorzien van mooie flensen. Uiteindelijk heb ik de frontjes netjes afgedraaid en passend gemaakt.
De pennen heeft Floris ook op lengte afgezaagd. De pennen heb ik vervolgens op maat gedraaid. Nadat ik de Ferulles had gemaakt heb ik alles in elkaar gezet na goed schoonmaken en met flux in te smeren heb ik de ketel in 1 keer in elkaar gesoldeerd met zilver. Hieronder is een foto gegeven van het resultaat.

Frame
Na de ketel, zijn we begonnen met het frame. Het frame is opgebouwd uit 4mm messing rechthoekig profiel. Floris heeft het messing op maat gezaagd, en in de freesbank zijn de kanten mooi haaks gemaakt. Daarna hebben we de gaten geboord op de freesbank zodat afstanden exact zijn en later de drijfstangen ook exact kunnen worden gemaakt voor een soepele loop.

Wielen
De wielen hebben we gedraaid uit een stuk staal. Hierbij hebben we het spoor 1 profiel aangehouden. De assen hebben we gemaakt van rond 3mm zilverstaal.
De drijfstangen heb ik gemaakt van 1,5mm metaalplaat. Een plaat heb ik gemonteerd op een stuk stevig multiplex. Na het boren van de gaten voor de drijfstangpennen, heb ik een profiel in de drijfstang gefreesd en heb ik de drijfstangen uitgefreesd.
Machine
De machine betreft een dubbelwerkende oscilerende machine. Via een ongeveer 1 op 2 tandwielverhouding drijft de machine de assen van de locomotief aan. De tandwielen heb ik van messing gemaakt. Bij een clublid van Nederlandse Modelbouw Vereniging Utrecht heb ik de tanden kunnen frezen.
De cilinder heb ik gemaakt uit een blokje messing. Dit is afwijkend van het oorspronkelijk ontwerp. Ik heb het gevoel dat het ook zo kan en dit leek mij handiger om te maken.


Op onderstaande foto is duidelijk de tandwieloverbrenging te zien.
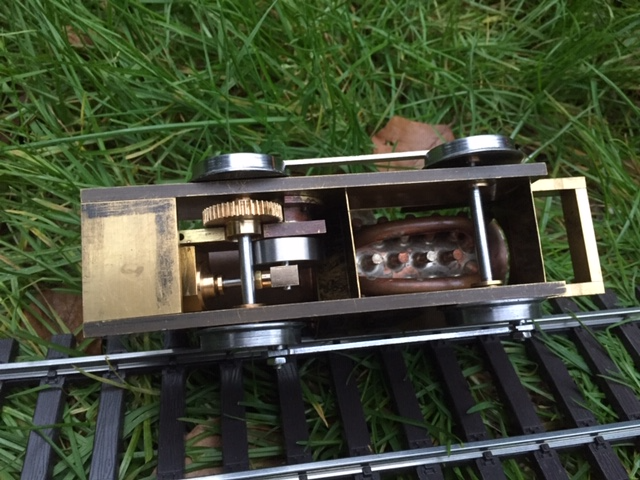
Vuurkist
De vuurkist heeft Floris voor een groot deel zelf gebouwd. Als eerste heeft Floris de vuurkistdelen op 0,5mm koperplaat afgetekend. Vervolgens heb ik de plaat geknipt. Met de vijl heeft Floris de platen op maat gemaakt.
Met wat hulp en aanwijzingen heeft Floris de plaatjes gebogen. Vervolgens hebben we de gaatjes geboord en heeft Floris de vuurkist met kleine klinknagels in elkaar gezet. Zoals op onderstaande foto te zien is, is het allemaal goed gelukt.

Brander
De brander heb ik opgebouwd uit 0,6mm koperplaat. De brander koppen zelf uit 12mm koperbuis. Het reservoir heb ik in fasen opgebouwd. Met klemmetjes heb ik het geheel bij elkaar gehouden tijdens de verschillende soldeerfasen. Achteraf heb ik het reservoir bijgevijld.

Ketel appendages
De vuldop, veiligheid en manometer aansluiting zijn gemaakt volgens tekening. De manometer wordt aangesloten met een varkensstaart krul voor de sifon ter voorkoming dat water in de manometer komt.
Voor de afsluiter heb ik een eigen ontwerp gemaakt.
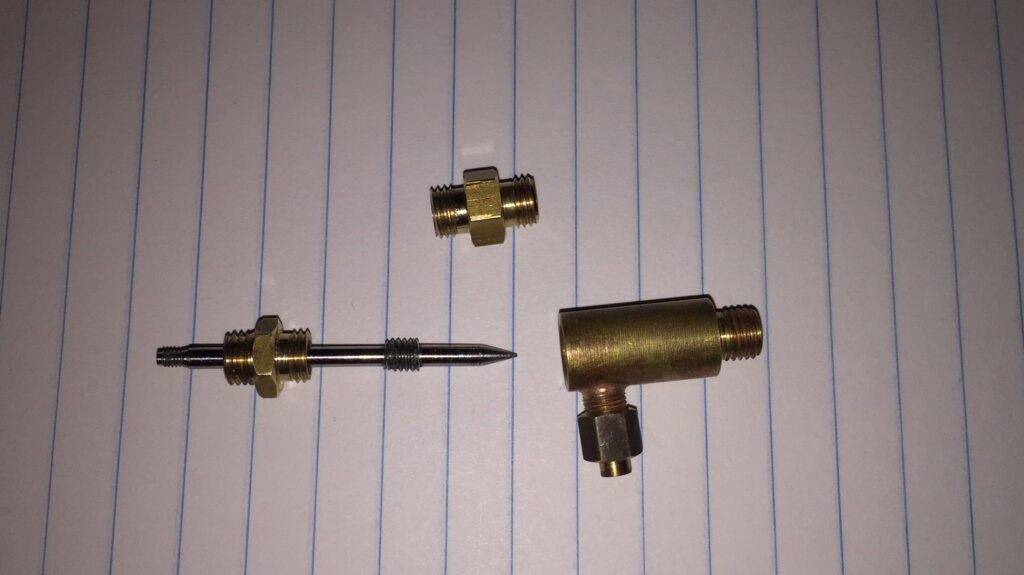
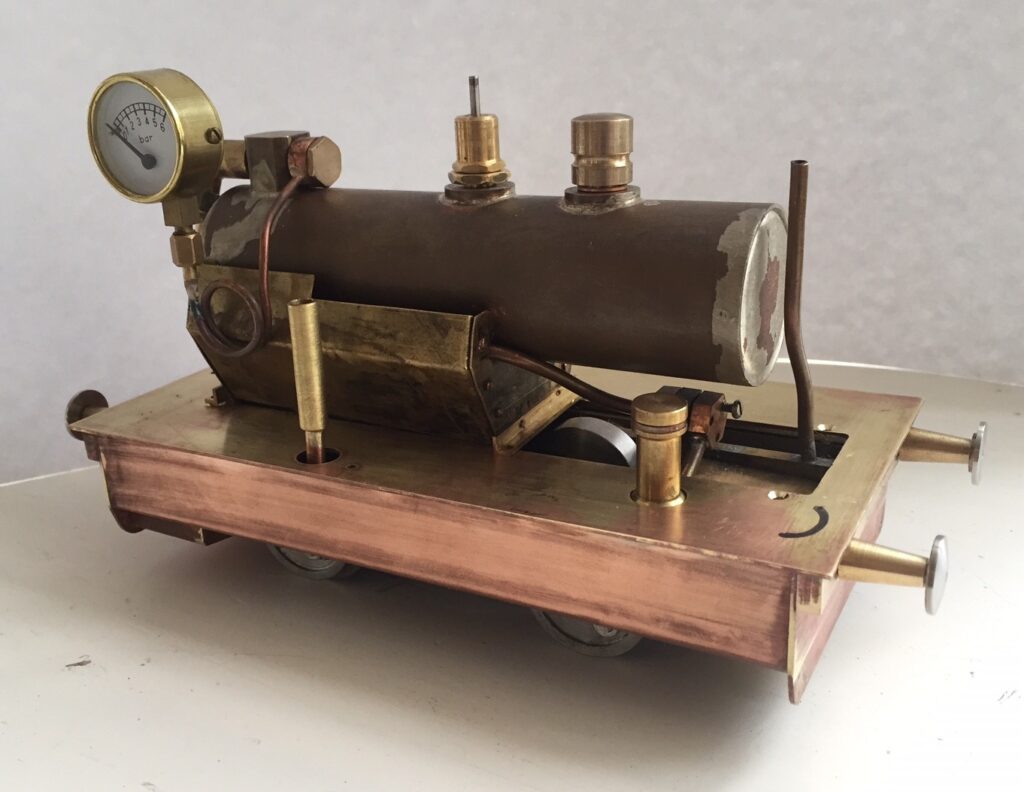
Voetplaat met buffers
Bovenop het frame komt een voetplaat met daaraan vast de bufferplaten en zijplaten. Op de bufferplaten komen de buffers met de haak.
Buffers
De buffer voetjes zijn gemaakt door Floris. Floris zijn eerste draaiwerk. Hij heeft hiervoor mijn oude Unimat 3 draaibank gebruikt. Samen met mij is hij bezig geweest de buffer voetjes te draaien. Opmeten, instellen van de draaibank, draaien, meten, etc.. De buffers heb ik samengesteld uit een 3mm staafje en de wat dikker staf voor de voorzijden. Hierbij heb ik eerst de achterkant afgedraaid, gaten geboord en de voorzijde afgezaagd. Daarna heb ik ze in elkaar geperst. Hieronder het resultaat.

Voetplaat
De voetplaat is opgebouwd uit verschillende delen. Nadat de delen op maat zijn gemaakt heb ik deze in een houten mal gefixeerd en in elkaar gesoldeerd met zilvertin. Bij het solderen begon het hout wel wat te smeulen, maar de functie van de mal bleef in takt. Na schoonmaken hielden we een zeer gelukte voetplaat over. Na het plaatsen van de buffers en het boren van gaatjes is de loc voor zover als mogelijk in elkaar gezet.
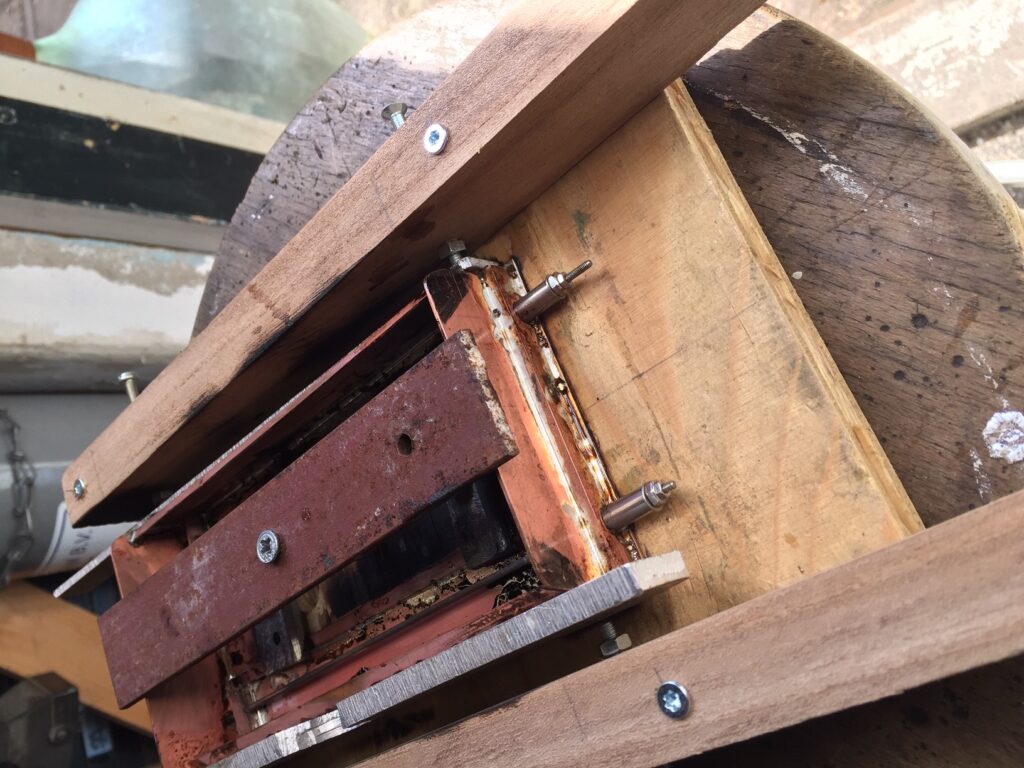

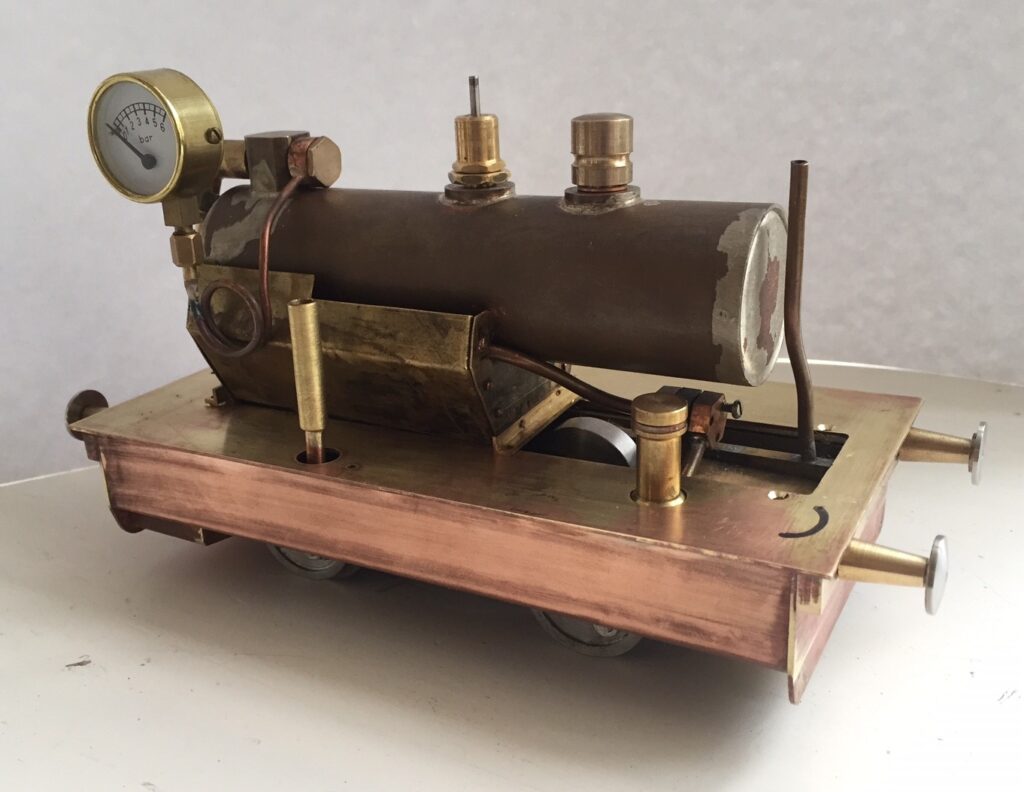
Machinistenhuis
Het machinistenhuis heb ik uit 0,8 mm messingplaat gemaakt. Hiervoor heb ik dankbaar gebruik gemaakt van de CNC freesbank van een clublid.
Aangezien het gehele ontwerp in OnShape is gezet, was het mogelijk om de zijkanten van het machinistenhuis naar een CNC machine te exporteren.


Het machinistenhuis heb ik in elkaar gezet met hoekprofiel van messing en kleine klinken. Het geheel heb ik daarna in elkaar gesoldeerd.
De ketelbekleding moet er ook voor zorgen dat de brandergassen langs de ketel richting de schoorsteen gaat. Om ervoor te zorgen dat de bekleding goed in elkaar blijft zitten, wordt de bekleding met zilver in elkaar gesoldeerd. Hieronder een afbeelding van het ontwerp van de ketelbekleding. Dit ontwerp wijkt van het originele ontwerp af omdat ik vulopening van de brandstof zeer dicht op de vuurkist en open vlam vond zitten. Met dit ontwerp is het vuur naar mijn mening beter afgeschermd.

Hieronder het resultaat van de eerste soldeerstap (linker twee foto’s) en de tweede soldeerstap (rechter foto).
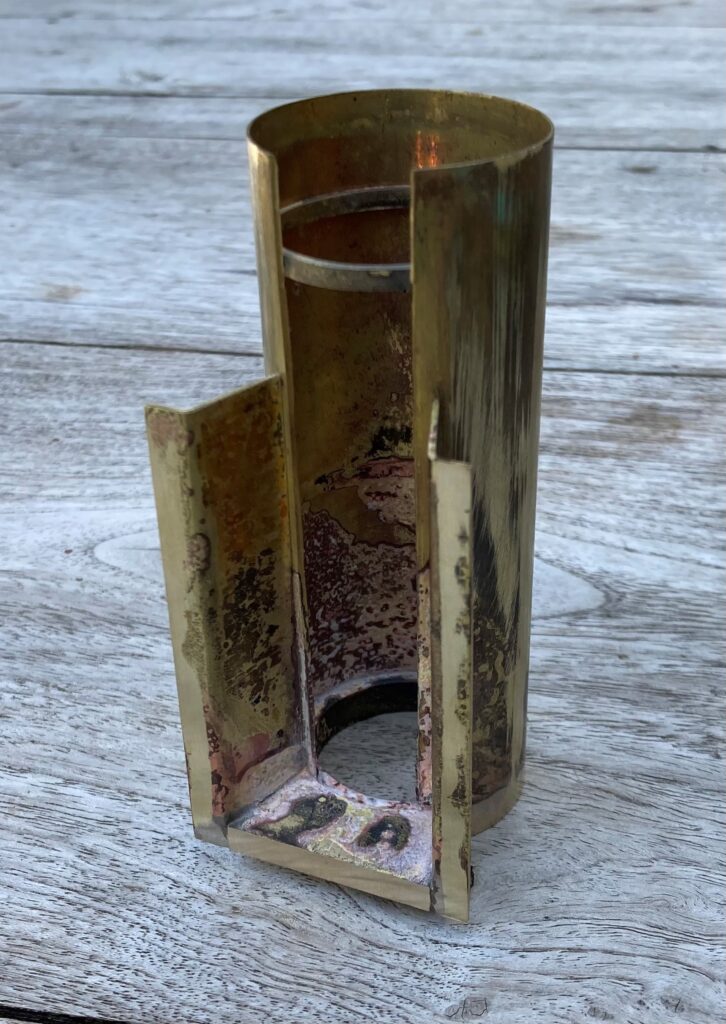
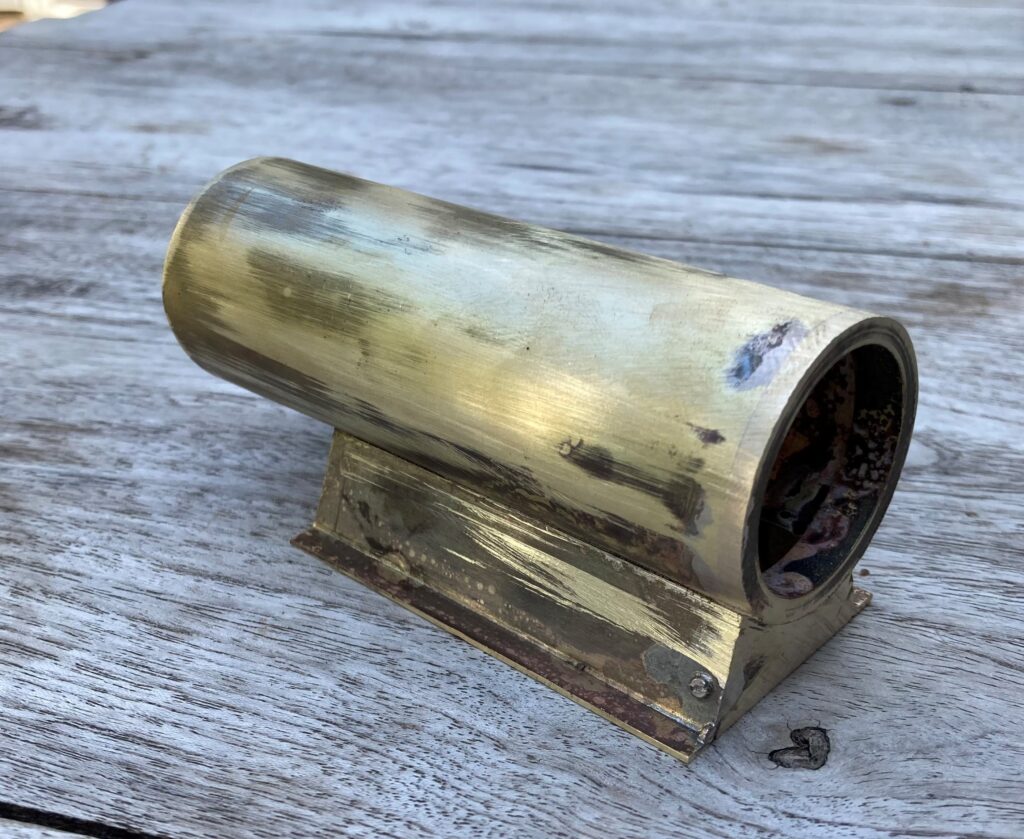

Op de linker foto zien we een ring zitten die nog eruit gaat en alleen voor het ontwerp voor wat steun zorgt.
Schoorsteen, dommen en kragen.
De kragen voor schoorsteen en de twee dommen heb ik uit 0.5 mm roodkoper plaat gemaakt. Hiervoor heb ik een aantal mallen gemaakt zoals hieronder afgebeeld.
De mallen bestaan uit drie delen:
- een houten deel die bedoeld is voor de vorm van de buitenkant van de kraag,
- een kunststof deel dat bedoeld is om de vorm om de ketelbekleding strak te houden en
- een pen deel dat bedoeld is om het gat door de kraag op de juiste maat te krijgen.

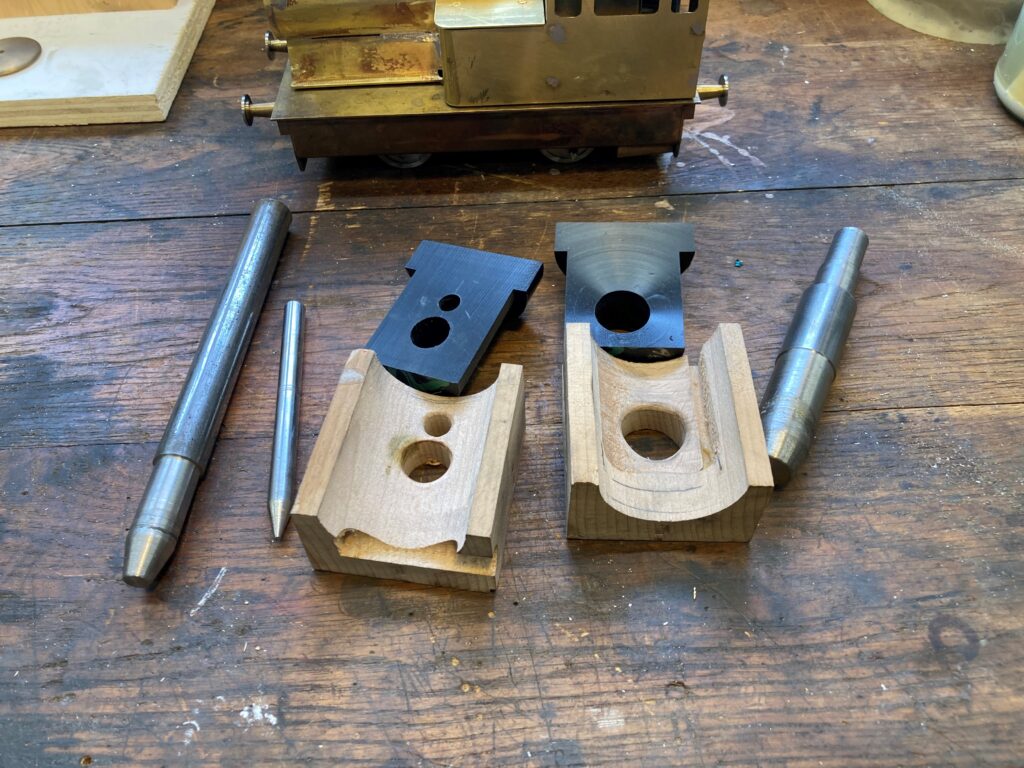
Voor de kraag knip ik een stuk koperplaat uit. In het midden breng ik een gat aan, en vervolgens gloei ik het plaatje uit. Nadat het plaatje is afgekoeld, leg ik het plaatje in de houten mal en druk ik met het kunststof deel van de mal de ketelvorm, vervolgens haal ik het kunststof deel van de mal er uit en druk ik de kraag met de pen er in. Ik herhaal dit totdat de pen nagenoeg door het gat van de kraag kan. Als laatste, na uitgloeien, leg ik de toekomstige kraag op het houten deel van de mal. zet daar het kunststof deel overheen en doe de ben door kunststof deel heen in de kraag. Daarna druk ik deze er doorheen en je hebt een mooie kraag. Het is belangrijk dat je iedere keer het koperen plaatje uitgloeit. Doe je dat niet, dan scheurt de kraag en kun je opnieuw beginnen.
Rijden en draaien

Nadat de voetplaat gereed was, kon de brander onder de locomotief bevestigd worden en kon de locomotief voor de eerste keer worden opgestookt. Na eerst wat problemen met de afdichting, reed de locomotief zijn eerste meter, maar de wind had veel invloed op het vuur waardoor de situatie onbeheersbaar werd. Daarom is gewacht met het verdere proefdraaien totdat de ketelbekleding etc. aangebracht was. Zoals op bovenstaande foto te zien is, is het bijna zover.
Voor het uiteindelijk kunnen proefrijden was het noodzakelijk de wielen goed vast te zetten. Hiervoor is het frame eerst zwart gemaakt en zijn de lagebussen aangebracht. Vervolgens is de onderzijde in elkaar gezet.
Bronnen
Informatie werd onder ander gehaald van Wikipedia en van de site nmld.locaalspoor.nl